5 Common Misconceptions About Warehousing and How to Avoid Them
T4
Introduction
Warehousing is a critical component of the supply chain, yet it is often misunderstood. Misconceptions about warehousing can lead to inefficiencies and increased costs. Understanding these misconceptions and how to avoid them can significantly enhance your business operations.
Misconception 1: Warehousing is Just Storage
Many people believe that warehousing is merely a place to store goods. However, modern warehousing involves much more than storage. It plays a crucial role in the logistics process, including inventory management, order fulfillment, and distribution.
To avoid this misconception, businesses need to view warehousing as a dynamic part of their supply chain strategy. Implementing technologies like warehouse management systems (WMS) can streamline operations and improve efficiency.
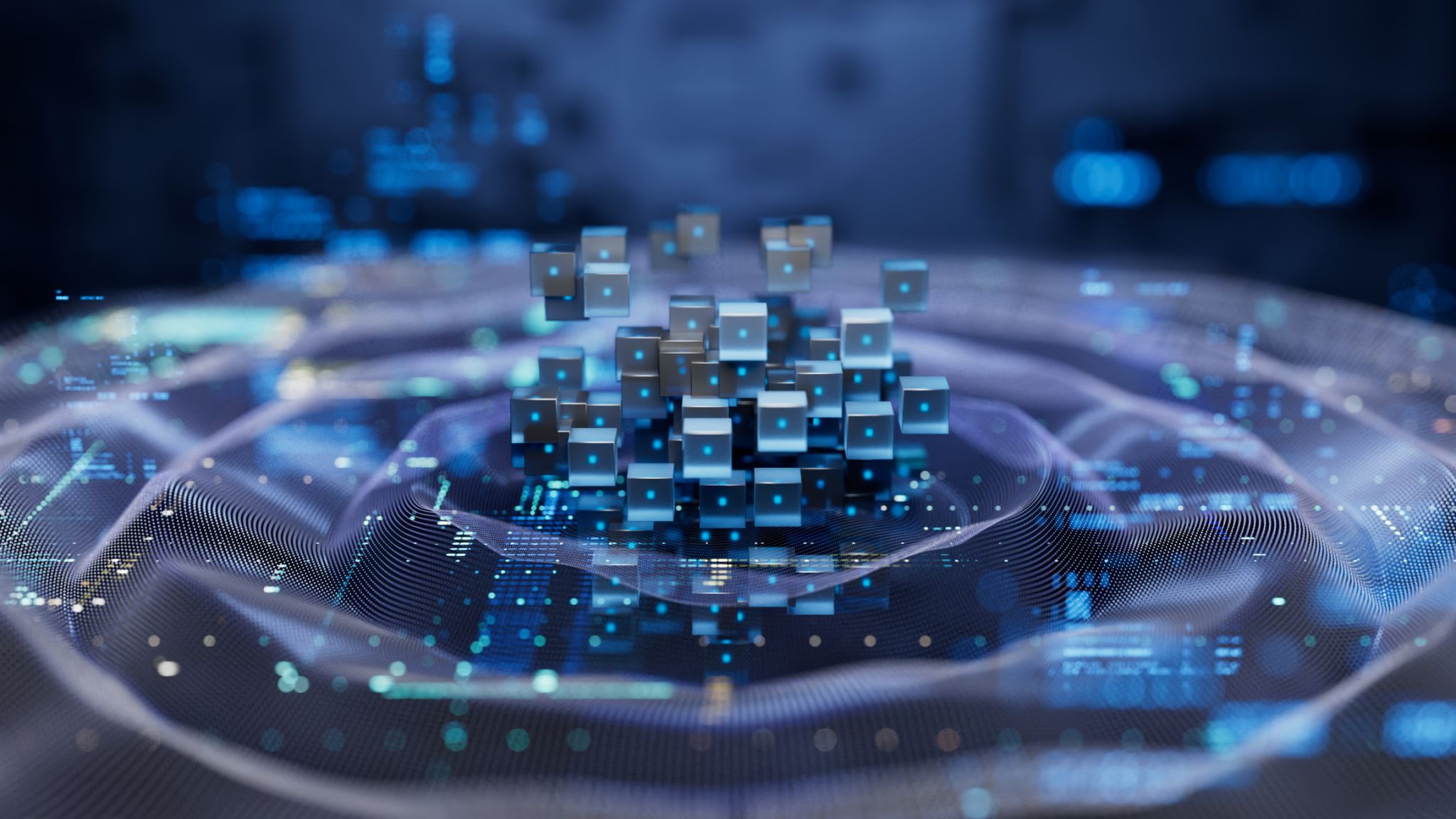
Misconception 2: More Space Equals Better Operations
It is a common belief that having more space automatically means better warehousing operations. While space is important, the efficient use of space is even more crucial. An oversized warehouse can lead to unnecessary costs without adding value.
Instead of focusing solely on size, businesses should prioritize optimizing layout and flow within the warehouse. Lean principles and smart layout designs can help maximize efficiency without expanding space unnecessarily.
Misconception 3: Manual Labor Is Cheaper Than Automation
Some companies hesitate to adopt automation, assuming manual labor is more cost-effective. However, automation can significantly reduce errors, increase speed, and improve accuracy, leading to long-term cost savings.
Investing in technologies such as automated storage and retrieval systems (AS/RS) or conveyor systems can enhance productivity and reduce operational costs over time.

Misconception 4: Inventory Accuracy Is Unachievable
Achieving high inventory accuracy is often viewed as an unattainable goal. In reality, with appropriate systems and processes in place, businesses can achieve impressive accuracy levels.
Implementing regular cycle counts and using advanced inventory management software can help maintain accurate inventory records, minimizing discrepancies and enhancing customer satisfaction.
Misconception 5: Warehousing Is Not Customer-Centric
Another misconception is that warehousing does not directly impact customer satisfaction. In truth, efficient warehousing operations can significantly enhance the customer experience by ensuring timely and accurate deliveries.
Businesses should focus on aligning warehousing processes with customer expectations, employing strategies like cross-docking and real-time tracking to improve service levels.

Conclusion
By understanding and addressing these common misconceptions about warehousing, businesses can optimize their operations and improve overall efficiency. Recognizing the strategic value of warehousing within the supply chain is essential for achieving competitive advantage.
Adopting a proactive approach by leveraging technology, optimizing space, and focusing on accuracy will lead to significant improvements in warehousing efficiency and customer satisfaction.